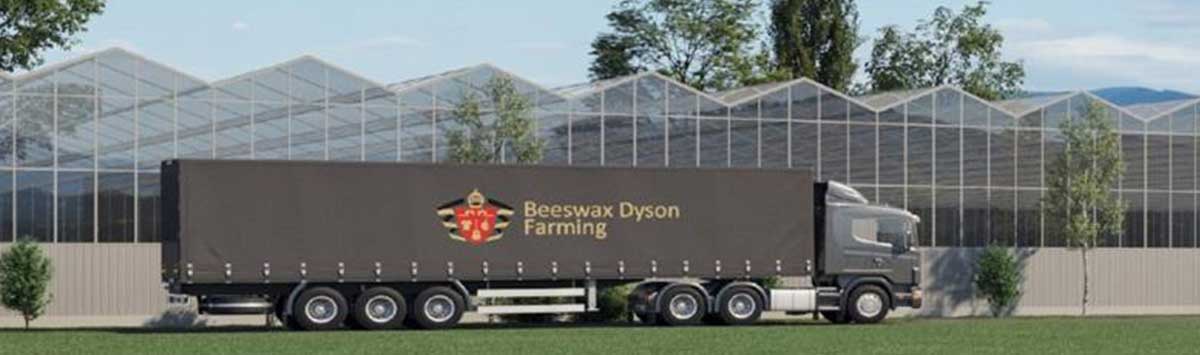
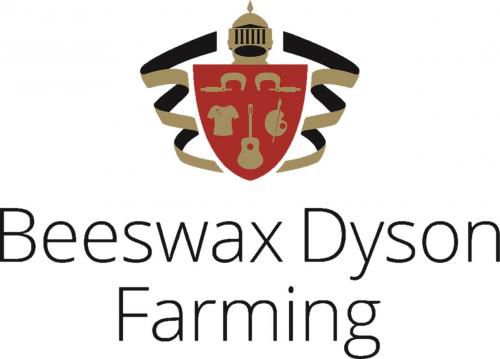
Automated Tracking System for Transport and Delivery
Background
Beeswax Dyson Farming is the agricultural subsidiary of Dyson Ltd. in the United Kingdom. With over $25 million in sales each year, Beeswax Dyson is a major component in the United Kingdom’s ag industry. It harvests, transports, and delivers crops across the entire country.
Background
Beeswax Dyson Farming is the agricultural subsidiary of Dyson Ltd. in the United Kingdom. With over $25 million in sales each year, Beeswax Dyson is a major component in the United Kingdom’s ag industry. It harvests, transports, and delivers crops across the entire country.
Challenge
Beeswax Dyson organizes its own transportation and delivery of harvested products, with an automated system that tracks work orders, jobs in progress, and signature of delivery through a secure desktop application. However, the digital solution was only utilized for destinations that were owned by Beeswax Dyson, or about 50% of their deliveries. For the 50% who were external customers, there was no provision for an automated solution. The drivers were responsible for creating a paper trail, generating paper receipts that had to be mailed back to verify successful arrival. This created errors, uncertainty, and inefficiencies.
Beeswax Dyson organizes its own transportation and delivery of harvested products, with an automated system that tracks work orders, jobs in progress, and signature of delivery through a secure desktop application. However, the digital solution could only be utilized for destinations owned by Beeswax Dyson, or about 50% of their deliveries. For the 50% who were external customers, there was no provision for an automated solution. The drivers were responsible for creating a paper trail, generating paper receipts that had to be mailed back to verify successful arrival. This created errors, uncertainty, and inefficiencies.
Challenge
Beeswax Dyson organizes its own transportation and delivery of harvested products, with an automated system that tracks work orders, jobs in progress, and signature of delivery through a secure desktop application. However, the digital solution was only utilized for destinations that were owned by Beeswax Dyson, or about 50% of their deliveries. For the 50% who were external customers, there was no provision for an automated solution. The drivers were responsible for creating a paper trail, generating paper receipts that had to be mailed back to verify successful arrival. This created errors, uncertainty, and inefficiencies.
Solution
To close the digital loop, Skyward developed a light-weight mobile application to substitute for the on-premises equipment located at official Beeswax Dyson terminals. The driver can simply grab a company iPad and log in to see the assigned jobs when delivering to an external client. Upon arrival, the driver is able to enter the delivery details and obtain a signature from the recipient. Even when out of range of a cell or wifi connection, the data is tracked and automatically delivered when re-connected. This eliminated the need to manage receipts and job printouts, manual reconciliation, and the occasional lost paperwork. Sometimes even small technology improvements can make jobs much easier and more efficient.
Solution
To close the digital loop, Skyward developed a light-weight mobile application to substitute for the on-premises equipment located at official Beeswax Dyson terminals. The driver can simply grab a company iPad and log in to see the assigned jobs when delivering to an external client. Upon arrival, the driver is able to enter the delivery details and obtain a signature from the recipient. Even when out of range of a cell or wifi connection, the data is tracked and automatically delivered when re-connected. This eliminated the need to manage receipts and job printouts, manual reconciliation, and the occasional lost paperwork. Sometimes even small technology improvements can make jobs much easier and more efficient.