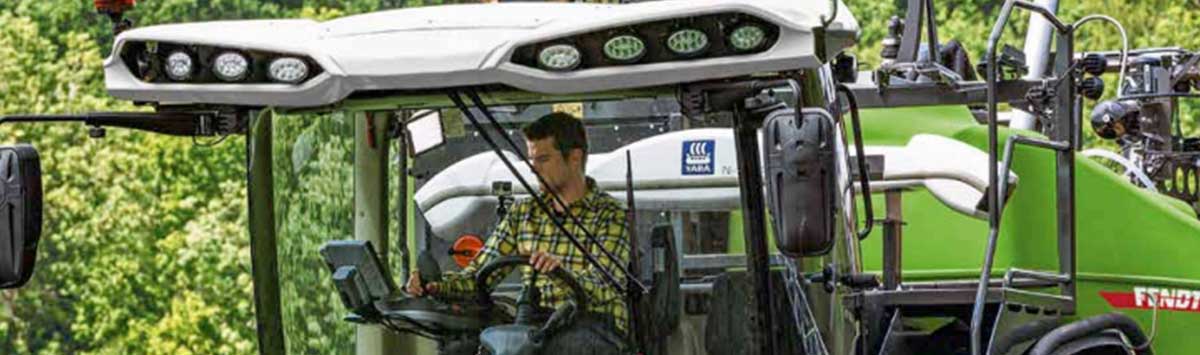
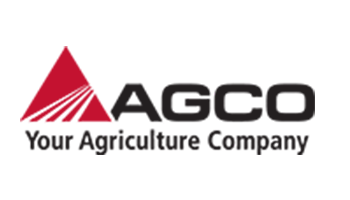
Time-Saving Work Order Management System
Background
AGCO is one of the largest farm equipment manufacturing companies in the world, with products that include spreaders and sprayers for efficient application of nutrients and protectants that improve crop yield. AGCO has invested heavily in smart farming technologies and a resilient supply chain to become a leading player in agribusiness.
Background
AGCO is one of the largest farm equipment manufacturing companies in the world, with products that include spreaders and sprayers for efficient application of nutrients and protectants that improve crop yield. AGCO has invested heavily in smart farming technologies and a resilient supply chain to become a leading player in agribusiness.
Challenge
It wasn’t that many years ago that AGCO and competitors were using manual methods such as sticky notes, spiral notebooks and tiny pencils, or just good old-fashioned yelling to communicate with farmers and operators in the field about tasks such as tilling, seeding, chemical applications or harvest operations. Given the number of farms and volume of equipment, it was inefficient both for company dispatchers and the equipment operators.
To better compete, AGCO needed an advanced solution to connect with farmers and field equipment that would improve service and save time. AGCO worked with Skyward to develop a software prototype that worked with existing mobile technologies.
It wasn’t that many years ago that AGCO and competitors were using manual methods such as sticky notes, spiral notebooks and tiny pencils, or just good old-fashioned yelling to communicate with farmers and operators in the field about tasks such as tilling, seeding, chemical applications or harvest operations. Given the number of farms and volume of equipment, it was inefficient both for company dispatchers and the equipment operators.To better compete, AGCO needed an advanced solution to connect with farmers and field equipment that would improve service and save time. AGCO worked with Skyward to develop a software prototype that worked with existing mobile technologies.
Challenge
It wasn’t that many years ago that AGCO and competitors were using manual methods such as sticky notes, spiral notebooks and tiny pencils, or just good old-fashioned yelling to communicate with farmers and operators in the field about tasks such as tilling, seeding, chemical applications or harvest operations. Given the number of farms and volume of equipment, it was inefficient both for company dispatchers and the equipment operators.
To better compete, AGCO needed an advanced solution to connect with farmers and field equipment that would improve service and save time. AGCO worked with Skyward to develop a software prototype that worked with existing mobile technologies.
It wasn’t that many years ago that AGCO and competitors were using manual methods such as sticky notes, spiral notebooks and tiny pencils, or just good old-fashioned yelling to communicate with farmers and operators in the field about tasks such as tilling, seeding, chemical applications or harvest operations. Given the number of farms and volume of equipment, it was inefficient both for company dispatchers and the equipment operators.
To better compete, AGCO needed an advanced solution to connect with farmers and field equipment that would improve service and save time. AGCO worked with Skyward to develop a software prototype that worked with existing mobile technologies.
Solution
The work order management system was a win for AGCO and its farm customers. The software allowed dispatchers to assign tasks, see where operators were and when, and communicate with them as needed.
A central user in the dispatch center listed the equipment and operators available to the company, created field outlines, and dispatched work requests to those operators. Each operator was provided a login to the web-based and mobile application. When work assignments were issued, the operator was notified. Operators could update their status, such as In Progress, Completed or Issues Encountered that needed attention.
In this way, AGCO’s dispatch center could monitor progress throughout the day and respond to problems as they arose, for a continuous flow of work as well as a continuous flow of support. The software system allowed farmers to realize higher up-time and lower overall cost of operating AGCO equipment to give the company a competitive edge.
Solution
The work order management system was a win for AGCO and its farm customers. The software allowed dispatchers to assign tasks, see where operators were and when, and communicate with them as needed.
A central user in the dispatch center listed the equipment and operators available to the company, created field outlines, and dispatched work requests to those operators. Each operator was provided a login to the web-based and mobile application. When work assignments were issued, the operator was notified. Operators could update their status, such as In Progress, Completed or Issues Encountered that needed attention.
In this way, AGCO’s dispatch center could monitor progress throughout the day and respond to problems as they arose, for a continuous flow of work as well as a continuous flow of support. The software system allowed farmers to realize higher up-time and lower overall cost of operating AGCO equipment to give the company a competitive edge.